I’ve been having a hard time getting out for a ride in the last couple months. Work is blown up and demanding mad hours (need to find a new job). Emmett is now walking. Cold weather has me tired all the time. There’s no end to things that need to be done around the house.
Got my chance yesterday. Almost folded when I woke up to see the 34F on the thermometer and the clouds in the sky. After breakfast and a snippet of sunlight, I decided I’d best take my chances. Good thing I did.
Per usual, I chose a general direction and tried my best to let my good road instincts guide me. Sometimes it works fabulously. Others, well, some of you have ridden through plenty of suburban sprawl hell zones that this city has so many mile of, with me. Sorry. Yesterday turned out right and I found some new great roads and routes to get out of Dodge with minimal foulness. I even wrote the names of the roads down on my fancy phone a few times during the day so I might get back there and continue scouting at some point.
I ended up at French Creek S.P. and Hopewell Furnace. I’d been camping at the former a few times but never had the pleasure of checking out the furnace. Wow. I had no idea. What a place. A system of sluices for carrying water from Hopewell Lake runs for miles through the woods to drive the water wheel for the furnace belows. The wheel house below is almost temple-like in its quiet and demand for calm. The coal barn and feed room set on the hill must be 100 feet above. Downstairs there were ten or more casting mold stations that appear to have been recently used. I wonder if they give demonstrations. The furnace is obviously not working, but there’s no reason they couldn’t make molds there at least. The pig iron troughs in the floor at the foot of the furnace were still full of old rusty iron. Stacks of pig iron lay about the building everywhere. Molds for frying pans and griddles and shirt irons too.
After a dynamite cup of coffee from a visitor center lobby vending machine (which spilled on me and took almost ten minutes) I made my way while I still had time. I suited up and pulled my ipod out of the tank bag. I spent the next few hours riding twisty back roads around Berks and Perkiomen counties through the blaze colored trees. Listened to Fleet Foxes and Fruit Bats and Black Keys. Perfect companion.
It was nice to be back on the BSA again. I finished this bike (again) in the Spring and spent the first couple months of the season riding it everywhere. Then for some reason I put it away in August and hadn’t been on it since. After pumping up the tires and changing the oil, she was a flawless ride. Nimble and perfect for this type of ride. You can flick this bike through the turns at 60mph just like a modern bike, or pretty close at least.
Got home by sundown and went out to dinner with my family.
Jason
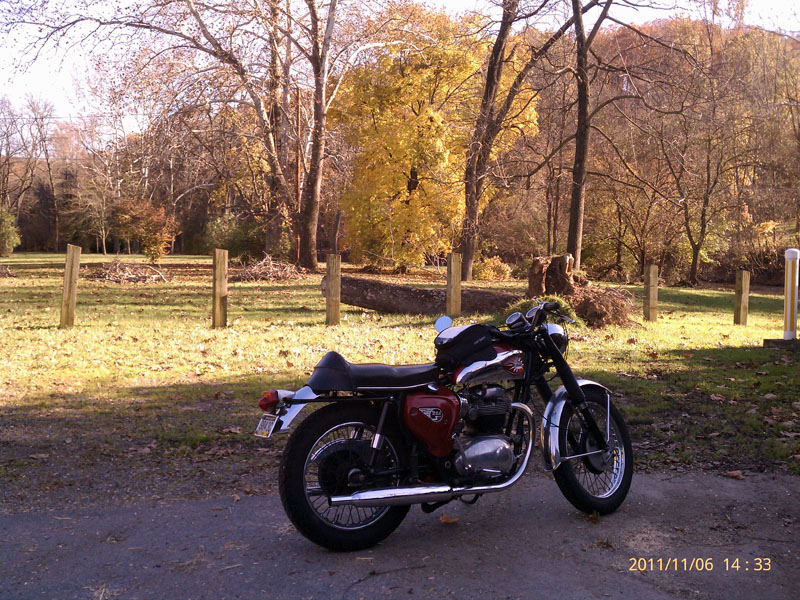
Manatawny Rd somewhere just below Oley, PA.
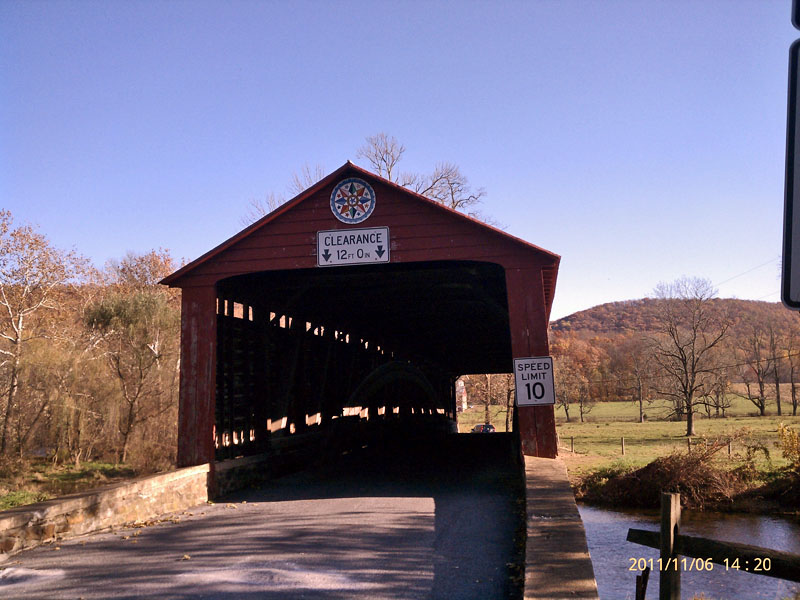
Covered Bridge Rd just outside of Pleasantville
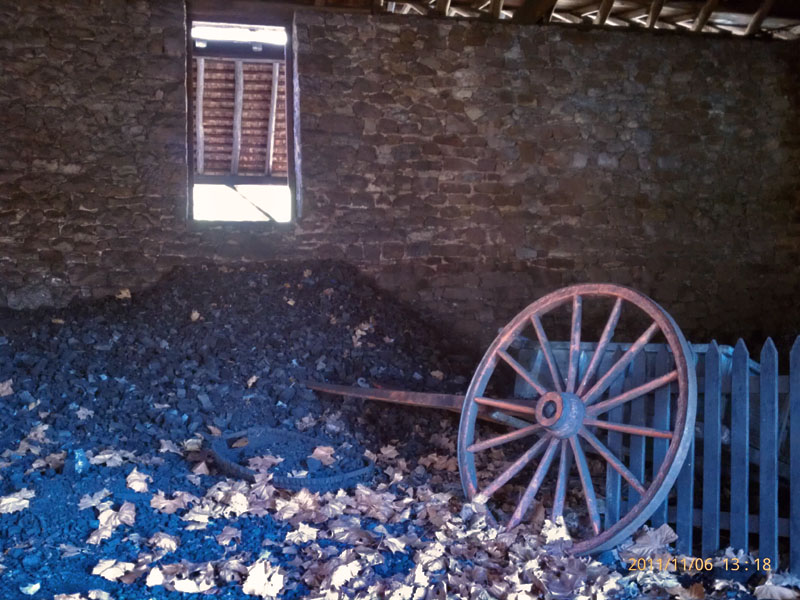
It wouldn't be Fall in PA without coal
Continue reading →